 |
Was Sie über Werkzeuge wissen sollten
|
|
Fräser: Hinweise zur Auswahl
Warum es gut ist, wenn Ihr Fräser möglichst viele Schneiden hat ...
- Die Schneide ist das Verschleißteil des Fräsers. Je mehr Schneiden der Fräser hat, umso mehr Schneiden teilen sich den Verschleiß, umso höher ist die Standzeit (Lebensdauer).
- Ein Fräser mit mehreren Schneiden läuft "runder" als ein solcher mit nur einer Schneide.
- Durch die größere vom Hartmetall eingenommene Querschnittsfläche beim Mehrschneider wird mehr Wärme in Richtung Spannzange abgeführt als beim Einschneider. Dies ist besonders wertvoll, wenn sonst keine Möglichkeit der Kühlung besteht.
- Je mehr Schneiden vorhanden sind, umso kleiner fallen die einzelnen Späne aus, umso glatter wird die Oberfläche.
Warum es gut ist, wenn Ihr Fräser möglichst wenige Schneiden hat ...
- Das Hauptproblem des (Schlitz-) Fräsens ist das Anbacken von Spänen und damit das Verstopfen ("Zusetzen") des Fräsers. Ist der Fräser erst einmal verstoft, so kann er keine Späne mehr fördern und die Vorschubkraft der Fräse bricht ihn ab. Dies passiert - je nach Material - meist lange bevor die Schneide verschleißt. Primär ist daher die Frage: "Wohin mit den Spänen ?" zu lösen. "Nach oben, bzw. nach hinten" lautet in der Regel die Antwort (Ausnahme: Linksdrallfräser). Dazu braucht man aber Platz (Spannut), um die Späne vorbei am "Fleisch" des Fräsers zu bewegen. Der Vergleich der Querschnitte verschiedener Typen zeigt klar, daß der Einschneider die größte offenen Fläche (= Größe der Spannut) aufweist, und daß diese abnimmt, je mehr Schneiden vorhanden sind.
- Je weniger Schneiden ein Fräser hat (und je spitzer diese sind), desto leichter ist das Eintauchen in die Oberfläche des Materials.
Was ist nun wichtiger?
Die Frage nach dem bestgeeigneten Fräser ist nur unter Betrachtung des zu bearbeitenden Materials zu lösen. Bei den in der Werbetechnik überwiegend eingesetzten Materialien wie Kunststoffen (PVC, Plexiglas, Kömacel, usw.), Holzwerkstoffen (Spanplatten) und NE-Metallen (weiches Alu, Alucobond, usw.) ist in der Regel der Einschneider im Vorteil, da hier das Problem der Schneidenerosion gegenüber der Verstopfungsgefahr zurücktritt. Bei sehr harten Kunststoffen und bei härteren Alu-Sorten (kurzspanend) ist der Zweischneider gut geeignet. Dreischneider empfehlen wir für sehr harte NE-Metalle (sehr harte Alu-Legierungen, Messing, ...) sowie für Eisenwerkstoffe.
|
|
Einschneider im Querschnitt
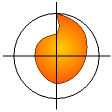
Der Einschneider weist eine große offene Fläche auf. |
Dreischneider im Querschnitt
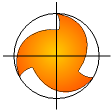
Die drei Schneiden beanspruchen sehr viel mehr Raum. |
|
Fräser: Betriebsparameter
Prinzipiell gilt:
- Je höher die Schnittgeschwindigkeit (vc = pi * ØS * n), desto glatter ("schöner") wird die Oberfläche. Gleichzeitig wächst mit der Schnittgeschwindigkeit aber auch der Verschleiß am Fräser.
- Empfohlene Schnittgeschwindigkeiten vc für Hartmetall - Fräser:
- Aluminium
langspanend: 100 - 300 m/min
kurzspanend: 100 - 200 m/min. (bei fehlender Kühlung: eher untere Grenze)
- andere NE-Metalle (Messing, Bronze, Kupfer, Zink, Rotguß) : 100 - 200 m/min
- rostfreier Stahl (VA): 80 - 120 m/min
- Thermoplaste: 50 - 150 m/min
- Duroplaste mit Füllstoffen: 100 - 150 m/min
GFK: 100 - 150 m/min
CFK: 150 - 300 m/min
- Empfohlener Vorschub fz pro Zahn (Schneide) und Umdrehung für Hartmetall - Fräser:
- Aluminium + andere NE-Metalle:
ØS 2 - 4 mm: 0.04 mm / U, ØS 5 - 8 mm: 0.05 mm / U, ØS 9 - 12 mm: 0.10 mm / U
- Thermoplaste:
ØS 2 - 4 mm: 0.05 mm / U, ØS 5 - 8 mm: 0.06 mm / U, ØS 9 - 12 mm: 0.07 mm / U
- Duroplaste, GFK:
ØS 2 - 4 mm: 0.04 mm / U, ØS 5 - 8 mm: 0.08 mm / U, ØS 9 - 12 mm: 0.10 mm / U
- Formeln: Drehzahl n:
- n [U/min] = (vc [m/min] *1000) / (3.14 * ØS [mm])
- Vorschub f: f [mm/min] = n * fz * z
Beispiel: Sie wollen mit einem Zweischneider ØS = 3 mm kurzspanendes Aluminium fräsen. Aus obigen Angaben: max. vc = 200 m/min.
max. Drehzahl n:
n = (200 * 1000) / (3.14 * 3) = 200.000 / 9.42 = 21230 U/min
Vorschub f:
f = 21230 * 0.04 * 2 = 1698 mm/min
|
|
Fräser: Geometrie und Maße
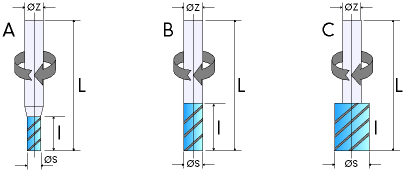
Form A: verjüngter Schneidendurchmesser: ØS < ØZ.
Form B: Schneidendurchmesser gleich Schaftdurchmesser: ØS = ØZ.
Form C: erweiterter Schneidendurchmesser: ØS > ØZ (nur bei Bohrern üblich)
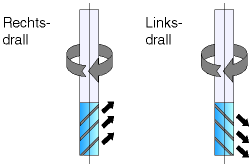
Rechtsschneider / Rechtsdrall (normale Form):
Förderung der Späne nach oben. Der Fräser hat die Tendenz, das Basismaterial hochzuheben ("Korkenzieher-Effekt").
Rechtsschneider / Linksdrall (Sonderform):
Förderung der Späne nach unten bzw. nach "hinten", also zur bereits freigelegten Nut hin. Der Fräser drückt das Basismaterial gegen den Tisch (umgekehrter "Korkenzieher-Effekt").
|
|
Eintauchtiefe
Welcher Stellenwert kommt der Eintauchtiefe zu ?
Die Eintauchtiefe spielt für die Ermittlung der Drehzahl und des Vorschubs nur eine sekundäre Rolle, da vor allem die Schneidgeometrie entscheidet wieviele Späne vom Werkzeug abgeführt werden können und mit welcher Drehzahl und Vorschub ein sauberer Schnitt im Material erzeugt wird.
Die Eintauchtiefe hat aber einen grossen Einfluss auf die Kräfte am Werkzeug. Bei einer zu grossen Eintauchtiefe entstehen Biegekräfte denen das Werkzeug nicht standhalten kann - es bricht ab. Mit einem dickeren bzw. kürzer eingespanntem Werkzeug-Schaft werden auch grössere Eintauchtiefen möglich.
Mögliche Vibrationen (insbesondere Resonanzen) verstärken bei grösserer Eintauchtiefe das Problem massiv.
Auch gibt es bei grösserer Eintauchtiefe durch Reibung eine grössere Wärmeentwicklung am Werkzeug, die vom Werkzeug abgeführt werden muss. Verkleben sich z.B. bei Kunststoffen die Werkzeuge mit Spänen, so hilft es die Reibung zu reduzieren, also:
Spindel-Drehzahl reduzieren, Vorschub erhöhen, Eintauchtiefe verringern
Auch hilft die Zuführung von geeigneten Kühl- und Schmiermitteln um die Temperatur-Grenzwerte im vertretbaren Bereich zu halten.
|
|
|